Over the course of several weeks, I have found myself drawn to the craft of pen-making. It is, I concede, an unconventional pursuit, perhaps sounding boring. My initial attempts involved slimline pens, but I soon progressed to the more expensive fountain pen.
The appeal of pen-making, contrary to what one might assume, lies in the size of the finished product. This allows for the use of exotic woods typically beyond the reach of the average woodworker. The reaction of recipients upon receiving a pen crafted from purpleheart or a burl is disproportionate to the object’s size. Many people do not recognise that wood can be so beautiful without any paints, for example.
I used the machines made available by my school to make these pens. Wood is first reduced to ‘blanks’, then further trimmed to to size brass inserts on a band saw. A lathe is then used to drill a central hole. The insert is glued in with epoxy and left to harden. The blank is then sanded to make it flush with the brass insert.
The shaping process involves mounting the blanks on bushings and subjecting them to the lathe. Various hand-held gouges are employed to achieve the desired form. This stage, whilst therapeutic, is not without its pitfalls. On occasion, the wood would suddenly explode. A man crying over his broken wood is not a sight to behold.
The penultimate stage involves finishes. I have used lemon oil, teak oil, linseed oil, various waxes, and shellac to impart various textures and sheens to the wood. Once cured, the components are pressed together using a wood vice.
This seemingly trivial hobby has, somewhat surprisingly, proven more educational in matters of wood, craftsmanship, precision work, and wood-turning than years of prior workshop experience.
Here are some pens I have made:
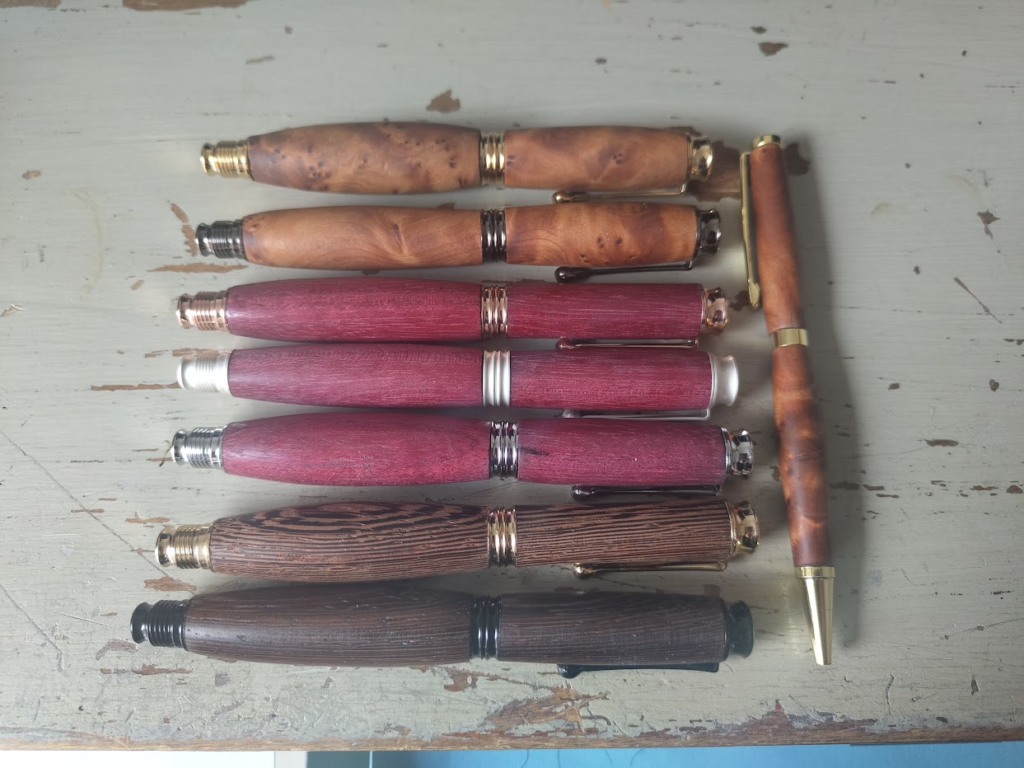
Leave a Reply